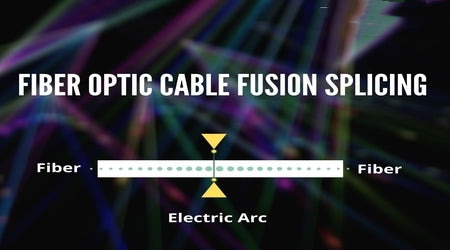
What is Optical Fiber Splicing?
Before we dive headfirst into all sorts of numbers and equations, let us paint a clearer picture of what splicing a fiber optic cable is.
Fiber splicing refers to the process of joining two optical fiber cables to create a longer link for optical signal. Thus, fiber splicing is what makes long-distance optical fiber communication possible. As such, fiber splicing involves couplers to which the end of one fiber bundle and the starting point of another optic fiber bundle are connected. The goal of fiber splicing is to ensure that any light passing through does not get reflected back from the splice point. Thus, adequate splicing can only occur if the two optic fiber bundles align together with proper geometry and strength.
What is Optical Fiber Splice Loss?
As we have already read, an optical fiber beam traveling through the core of an optical fiber cable will gradually lose its signal strength. This phenomenon is called attenuation or fiber optic loss. While there are many ways it could occur, attenuation also happens in the form of optical fiber spice loss.
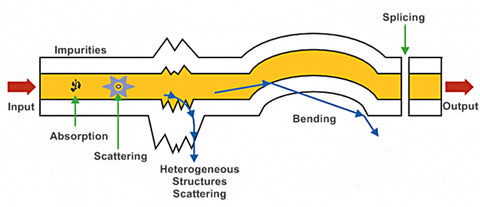
The size of the loss is an important technical indicator of the optical fiber fusion splicer. The lower the loss, the higher the precision of the machine, which can support longer distance fusion splicing. The more perfect the fusion point, the longer the service life.
However, many fusion splicers are optical fiber fusion splicers assigned by the company's construction team or the telecommunications bureau. The optical fiber fusion splicer has been fixed and cannot be replaced, so we need to rely on technical operation specifications during the construction process to improve the quality of fusion splicing and reduce losses.
The main points to note are:
1. The cutting angle of the fiber is very important.
Nowadays, most optical fiber fusion splicers are fully automatic fusion splicing.
So you can set the splicing mode to semi-automatic and let the fiber push to the screen to display the angle. If the angle meets the standard, press the splice button. If it does not meet the standard, you can re-cut the fiber.
For the best fusion splicing effect, it is recommended that the fiber cutting angle be around 0.5°.
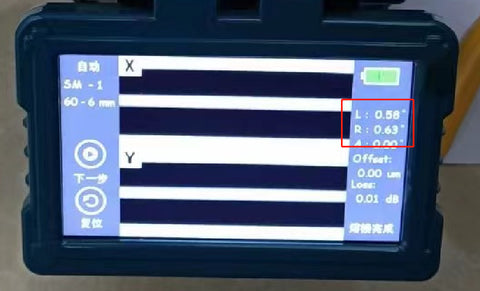
2. The machine performs discharge corrections on a regular basis.
Discharge correction is mainly for the machine to adapt itself to the working environment and fine-tune itself, so that the discharge voltage, current and other aspects of the optical fiber fusion splicer are most suitable for the working environment at that time, so as to achieve the best fusion splicing state.
Doing discharge corrections every time will help the machine maintain the best welding state, which can effectively reduce the huge loss caused by changes in external temperature and humidity.
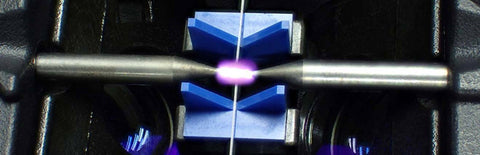
3. Regularly replace the electrode rod
The discharge of welding is mainly through the work of the electrode rod. Long-term use will cause the electrode rod to age slowly. Generally, the life of the machine electrode rod is about 3000 cores, and some better machine electrode rods can use 3000 to 6000 cores. Therefore, after the machine is used for a period of time, it is necessary to pay attention to the loss of the lower electrode rod and replace it in time to avoid the problem of increased loss.
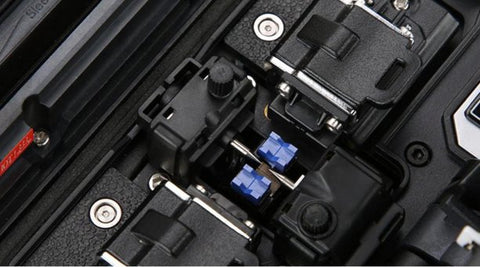